Computational Fluid Dynamic (CFD) Modeling
- Predicting heat and contaminant exposure levels
- Evaluating performance of ventilation systems in process plants
- Predicting airflow patterns and contaminant migration paths
- Optimizing primary and secondary capture hood performance
- Predicting and optimizing process gas mixing and combustion
- Evaluating burner configuration and selection
Melt Shop Overall Geometry
The geometry was developed in the Phoenics package model editor using drawings provided by the melt shop
- Provides a Quantitative Estimate of Fume Capture
- Provides a Quantitative Estimate of Temperature at any Elevation Inside Building
- Model Validated Using Field Measurements
- Able to Test Many Scenarios Efficiently
- Effects of Wind Direction and Ambient Temperature on Cross Drafts and Hood Fume Capture Performance
Charge Existing
Charge Future
Gas Cleaning Services
GCT provides gas cleaning services such as process gas handling, fugitive emission control, bulk material handling, and more.
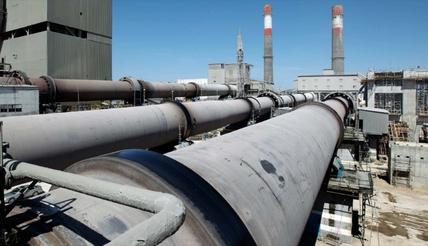
Process Gas Handling &
Cleaning System Design
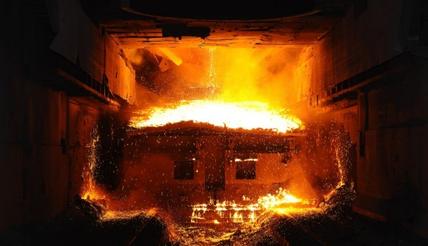
Fugitive Emission
Control
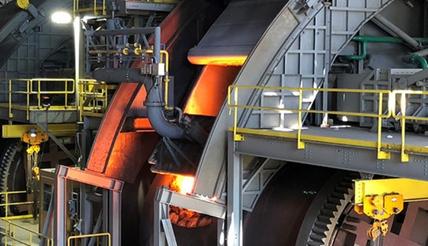
Drummond-GCT
Water Cooled Head
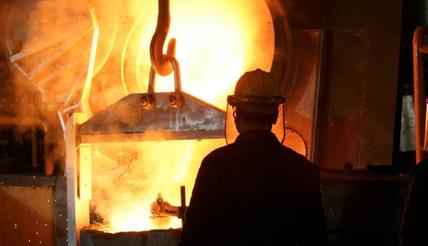
Process Vessel
Design
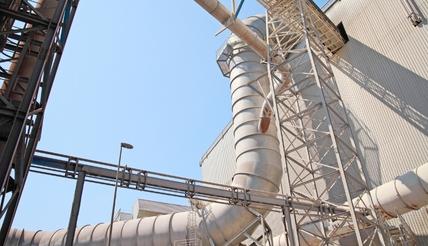
Existing Asset Life Cycle
Optimization
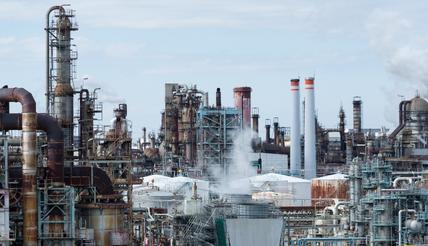
Process Evaluation &
Optimization
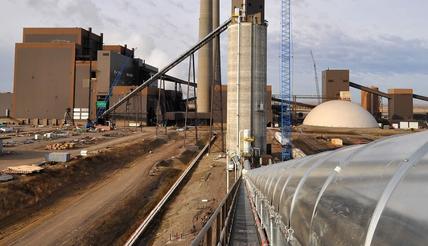
Bulk Material Handling
System Design
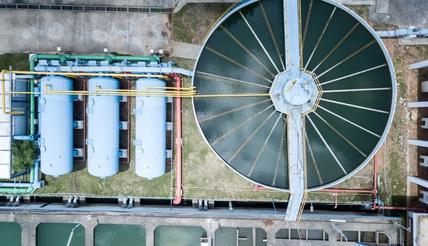
Water & Wastewater
Treatment
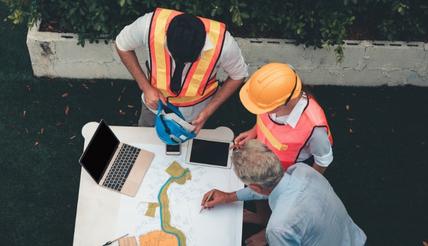
Project Development
Services
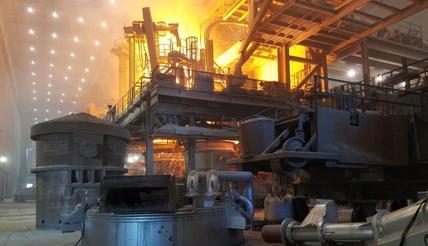
Technology Commercialization &
Integration
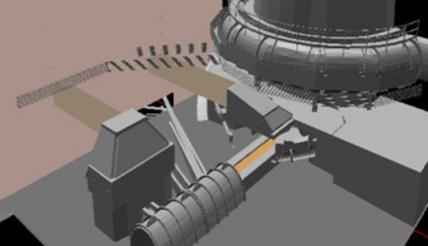
Computational Fluid
Dynamic Modeling
Energy
Services
GCT provides waste heat recovery solutions, plant energy audits, decarbonization roadmap development, and many more energy services.
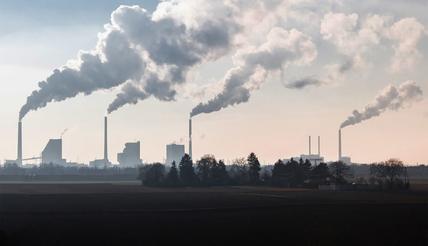
Energy
Optimization
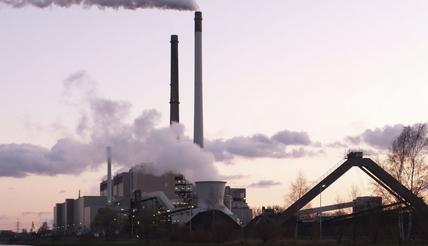
Plant Energy
Audits

Fuel Conversion
Solutions
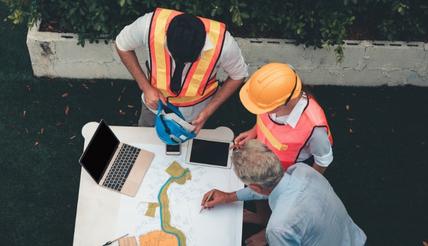
Project Development
Services
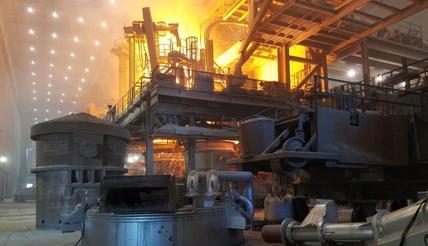
Technology Commercialization
& Integration
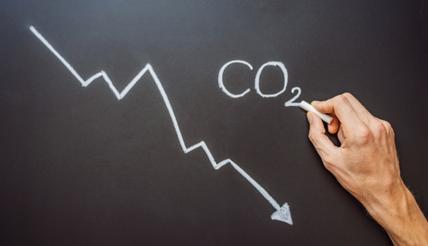
Decarbonization Roadmap
Development
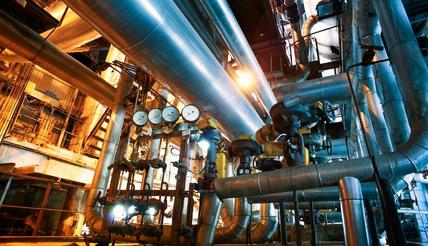
Waste Heat
Recovery Solutions
Hydrogen
Services
GCT is proud to provide hydrogen services for applications such as metallurgical reduction, industrial thermal heat, and power generation.
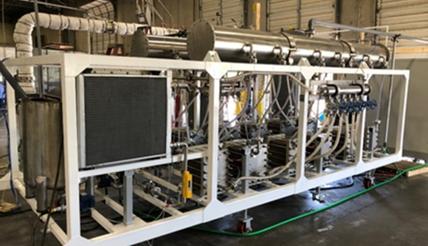
Hydrogen Technology
Development
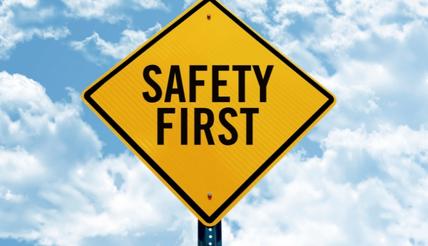
Hydrogen Risk & Safety
Management
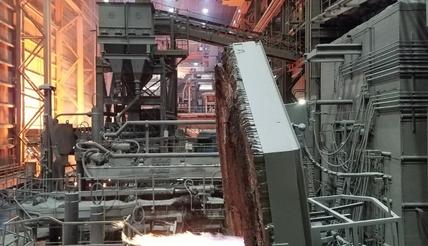
Hydrogen Technology
Integration & Implementation
Let's Make The World a Better Place, Together
Follow Us
GlossyFox Web Design